- Waste management in Japan
- Circular economy in Japan
- Waste management in Asia
- Disaster waste management
Solid Recovered Fuels for Paper Mills in Japan and Overseas and Their Quality
English translation: January 2023
Paper mills usually have a facility called boiler to generate steam. The steam is used to produce electricity for the equipment on the premises and heat for drying paper. Timber is one of the most indispensable raw materials for paper production. Certain types of wood that are unsuitable for paper production are sometimes used as a biofuel for boilers. Not only wood but also plastic and paper wastes from households can be used as refused derived fuels (RDFs) for boilers as they burn easily. However, if the wastes contain high concentrations of hazardous substances such as chlorine and mercury, they cannot be used as RDFs. A high chlorine content will cause corrosion of boilers. If the concentration of mercury is high, it will be released into the environment as flue gas when RDFs are incinerated. These substances may have harmful effects on human health and the environment. In Europe, the European Union has established the quality standard (i.e., EN: European Norm) for a type of RDF called “solid recovered fuel (SRF)” to define its flammability and permissible chlorine and mercury content for smooth distribution.
Japanese paper mills have been using RDFs that are mainly produced from industrial paper and plastic wastes. In Japan, this type of RDF is called “refuse derived paper and plastics densified fuel (RPF),” and its quality standard has been defined by the Japanese Industrial Standards (JIS). Only high-quality RPF with high flammability and low chlorine content can fulfill the JIS requirements. Although we cannot easily compare the standards between JIS and EN, certain SRF categories with much lower quality than JIS standard exist in Europe. Then, what types of solid recovered fuels have been used in European paper mills?
Finland is a country with a large pulp and paper sector, and we can find paper mills across the country. A paper mill is also found in a small town about 250 kilometers away from the capital Helsinki. In its premises, a combined heat and power (CHP) plant was installed and started its operation in 2014 (Fig. 1) with the use of some 90,000 tonnes of SRFs every year as part of the fuels to produce electricity and heat. This plant is one of the CHP plants that use the largest amount of SRFs in the country. The plant supplies not only electricity and heat to the paper mill but also excess heat to district heating systems.
The most distinctive feature of the SRFs in Europe is their shape. It differs from the RPF that is produced in Japan. Japanese paper mills mainly use a material called “pellet” that is produced by consolidating wastes at high temperature. Finnish paper mills, on the other hand, use a material called “fluff” that is made by crushing and shredding the wastes into certain sizes, not by consolidating them (Fig. 2). The Finnish SRFs also differ from the Japanese RPF in terms of their permissible content of chlorine, one of the hazardous substances. For example, we found that a Japanese paper mill accepts only the RPF whose chlorine content is less than 0.3%; it uses only the high-quality fuels derived from wastes. By contrast, the paper mill in Finland accepts SRFs if their chlorine content is less than 1%. Another difference is the types of wastes used to make the fuels. Japanese paper mills use the RPF made only from industrial waste while the paper mill in Finland uses a large amount of SRFs made from a wide variety of wastes including commercial and municipal wastes in addition to industrial waste. This means that the CHP plant in Finland has been not only supplying electricity and heat to the paper mill but also actively and effectively utilizing the diverse wastes generated in the surrounding areas although they may not have high quality.
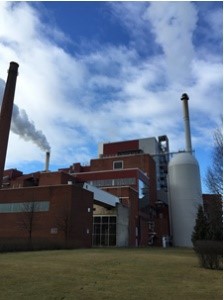
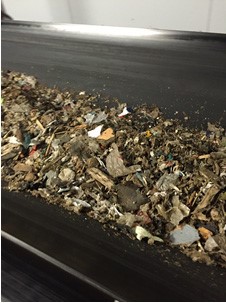
As mentioned earlier, higher content of chlorine is more likely to cause corrosion of the facilities and increase the maintenance cost. Some equipment in the CHP plant in Finland can potentially have shorter lifetime compared with that in similar plants in Japan. Deciding which RDFs to use depends on each company's operational strategy, but the level of their quality can be judged using “standards” as one of the criteria. In order to prepare for international standardization of SRF, the International Organization for Standardization (ISO) established a technical committee (ISO/TC 300) in 2015 that consisted of six working groups (WGs) (Table 1). The researchers of the National Institute for Environmental Studies have been participating in the ISO/TC 300 as Japanese experts to present Japan’s experience with the establishment of JIS for RPF and the production and use of the RDF made from municipal waste. Through this work, we have been encouraging the ISO/TC 300 to consider the knowledge obtained from Japan’s experience and reflect them in SRF’s international standard. We will continue our efforts to develop mechanisms that can contribute to the sound production, distribution and use of SRFs in the Asian region.
Working Group(WG) | Theme |
---|---|
WG1 | Terminology and quality assurance |
WG2 | Specification and classes |
WG3 | Sampling and sample preparation |
WG4 | Physical and mechanical tests |
WG5 | Chemical tests and determination of biomass content |
WG6 | Safety of solid recovered fuels |